Air Poppets Application
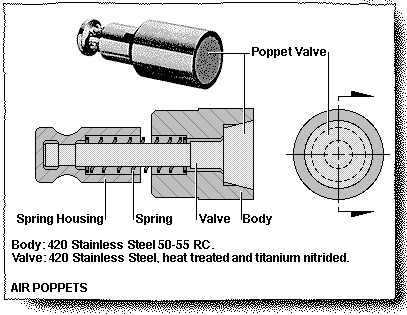
Air poppet valves are designed to assist the ejection process. They are precision engineered to remedy the vacuum problem often encountered during the molding of thin walled or deep draw parts, such as buckets. Air flow is timed with ejection cycle to force a tapered valve off its seat and break the vacuum seal holding the part. Typical installations are a standard “A” Series mold base with ejector pins or a “X” Series mold base using a stripper plate for part ejection. The actuation animation shows the stripper plate ejection method. Note: Air poppets should not be the sole means of part ejection.
Air Poppets Actuation
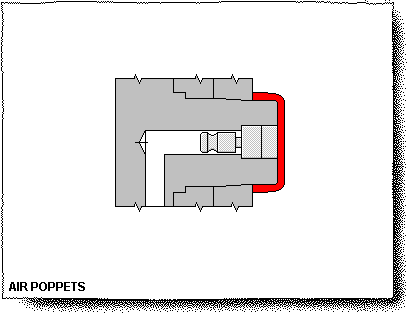
After molding, the ejection half of the mold travels back until it reaches its stop position. When the part is ready for ejection, pressure to the air passage of the poppet valve and timing of the machine ejection are then activated just prior to the ejector pins contacting the part. Control valves and limit switches provide the timing. The poppet valve relieves the vacuum and the plate ejector forces the part off the core and out of the mold. Although the spring has returned, the air flow to the poppet valve must be fully relieved to the atmosphere after each cycle..
Page 9 of 11